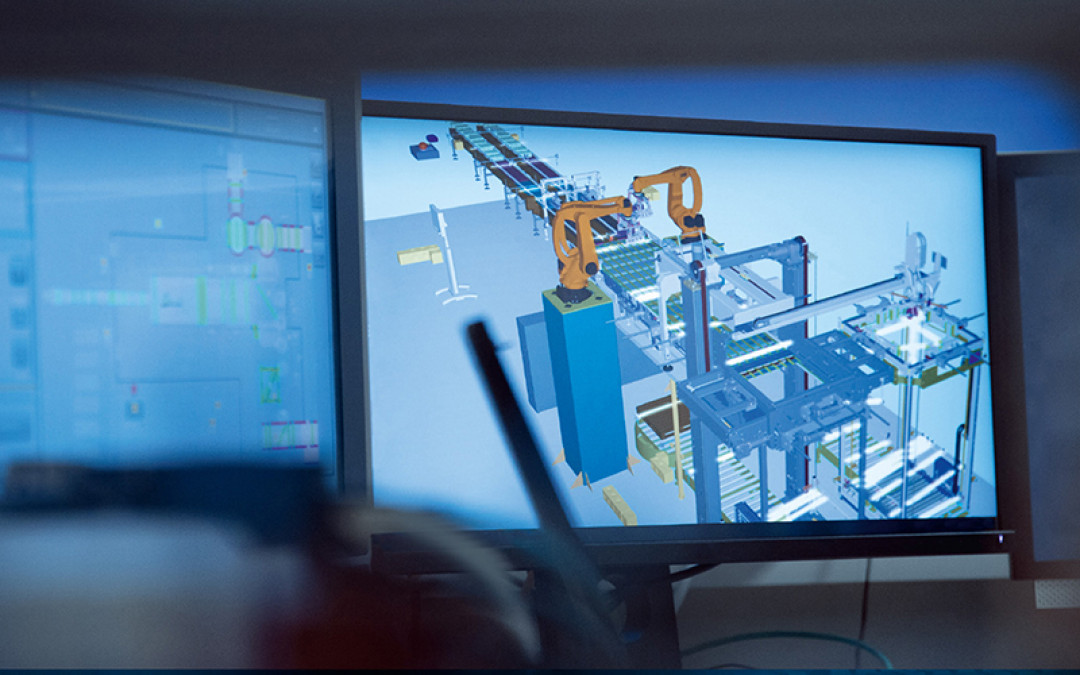
Digitaler Zwilling bildet Anlage bis ins letzte Detail virtuell ab
KHS nutzt bereits heute Modelle, um die Inbetriebnahme von Maschinen und Transportanlagen virtuell abzubilden. Mithilfe digitaler und smarter Technologien vernetzt und automatisiert KHS Produktionsprozesse Schritt für Schritt, damit Maschinen, Produkte und komplette Anlagen effizienter miteinander kommunizieren und zusammenarbeiten.
„Insbesondere der sogenannte digitale Zwilling ermöglicht die Verlagerung in den virtuellen Raum, indem er alle Phasen des Lebenszyklus einer Maschine verfolgt und abbildet. Sämtliche Produktionsprozesse und Produkte lassen sich dadurch virtuell simulieren“, sagt Stefan Diesner, Head of Product Center Palletizing. Auf dem Rechner erscheinen alternative, optimierte Fertigungsabläufe. Eine der wichtigsten Voraussetzungen dafür ist die Durchgängigkeit des Engineerings über die gesamte Wertschöpfungskette, um sogenannte Datenbrüche an den Schnittstellen der Ingenieursdisziplinen Mechanik, Elektrik und Software zu vermeiden. Anders als heute vielfach üblich, wird dabei nicht sequenziell, also nacheinander und separat gearbeitet. Im Idealfall arbeiten alle Bereiche übergreifend parallel an der Umsetzung eines Projekts und nutzen ein gemeinsames Datenmodell – die Basis für den digitalen Zwilling, der eine Anlage virtuell bis in jedes Detail abbildet und exakte Simulationen erlaubt.
Für einen Anlagenbauer wie KHS, der nicht nur eine Vielfalt verschiedenster Maschinen herstellt, sondern bei dem die Bereiche Entwicklung und Konstruktion auch noch geographisch auf mehrere Standorte verteilt sind, stellt das eine große Herausforderung dar. Schon seit 13 Jahren beschäftigen sich die KHS-Ingenieure des Product Centers Palletizing in Worms mit der virtuellen Abbildung von Maschinen und Anlagenteilen sowie deren Simulation. Insbesondere im Bereich von Logistikanlagen wie Palettierern oder Transporteuren bietet sich die Durchführung einer Simulation oder einer virtuellen Inbetriebnahme an.
„Unser Ziel ist es, mit der Ausweitung der virtuellen Inbetriebnahme Durchlaufzeiten weiter zu reduzieren und Fehlerkosten zu senken“, erklärt Diesner. Um den Umfang der Ersparnis abzuschätzen hilft es, sich die Zehnerregel zu vergegenwärtigen. Diese besagt, dass die Kosten für die Fehlerkorrektur um den Faktor zehn ansteigen, je später ein Fehler im Prozess entdeckt wird. Kann also ein Fehler erst in der Werksinbetriebnahme gefunden und ausgeräumt werden, ist der finanzielle Aufwand zehnmal höher als wenn die Korrektur schon in der Softwarekonstruktion während der virtuellen Inbetriebnahme erfolgt.
Ein weiteres Ziel der aktuellen Arbeit ist es, den Aufwand für die Realisierung der virtuellen Inbetriebnahme zu reduzieren. Eine Grundvoraussetzung hierfür ist die Datenkonsistenz. „Bei der virtuellen Inbetriebnahme haben wir das Thema Datendurchgängigkeit selbst in der Hand“, erklärt Diesner. „Alle Daten werden in unserem Werk erzeugt und vorgehalten, bisher allerdings noch in unterschiedlichen Systemen. Hier sind weitere Schritte erforderlich, bevor diese Daten in einem Werkzeug für ‚Virtual Engineering‘ einschließlich der Simulation effizient und bidirektional zur Verfügung stehen. Ist das erst einmal geschafft, können wir nach Kundenanforderungen konfigurierte oder angepasste Maschinenkonstruktionen schnell und effizient am Bildschirm in Betrieb nehmen.“
KHS
Schlagworte
AnlagentechnikDigitalisierungMaschinentechnik