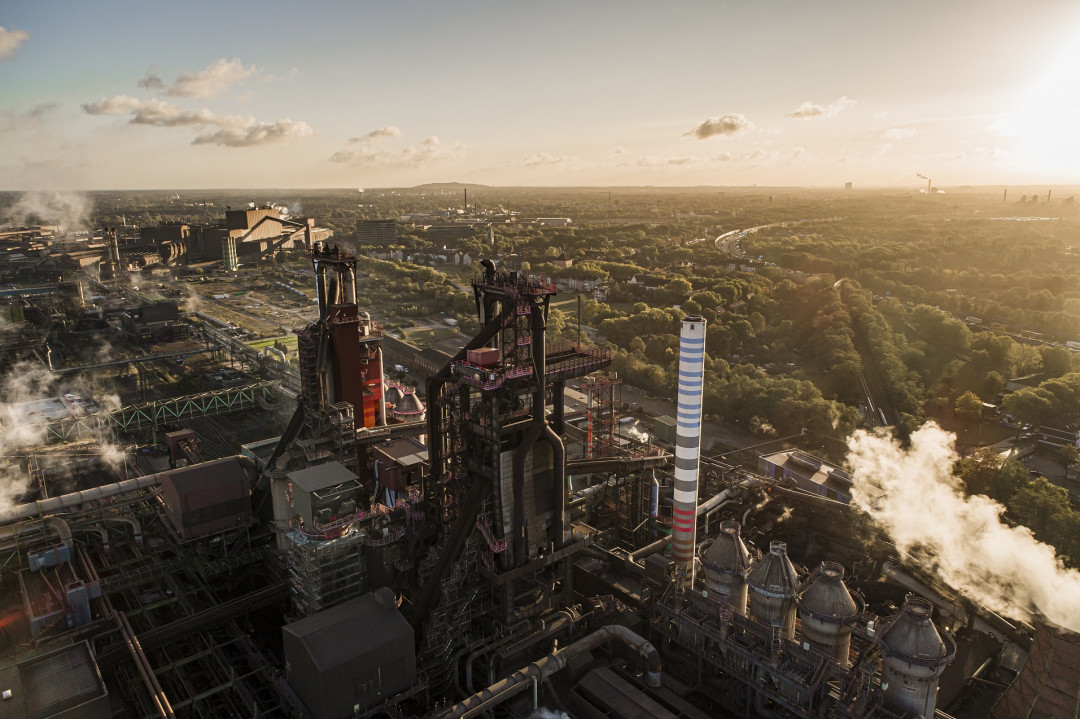
Reallabor der Energiewende H2Stahl startet am Standort Duisburg von thyssenkrupp Steel
Das vom Bundesministerium für Wirtschaft und Klimaschutz mit 37 Millionen Euro geförderte Reallabor der Energiewende geht in die Umsetzung. Beim Start von H2Stahl in Duisburg stellten die Konsortialpartner thyssenkrupp Steel, Air Liquide Deutschland und das VDEh Betriebsforschungsinstitut (BFI, Projektkoordination) nun die Weichen für die ersten Schritte. Arbeitspakete sind zum einen die Ausweitung des Wasserstoffeinsatzes auf den gesamten Hochofen 9 inklusive des Baus einer Pipeline zur Erprobung des großindustriellen Einsatzes von Wasserstoff in der Stahlherstellung.
Zum anderen wird mit dem Bau und versuchstechnischen Betrieb einer Direktreduktions-Versuchsanlage der Technologiesprung in die wasserstoffbasierte, klimaneutrale Roheisenproduktion erprobt. Die Gesamtkosten des auf fünf Jahre geplanten Projekts liegen im hohen zweistelligen Millionenbereich.
Am 11. November 2019 hat thyssenkrupp Steel als erstes Unternehmen weltweit Wasserstoff in einen laufenden Hochofen eingeblasen. Der Wasserstoff ersetzt dabei Kohlenstaub alszusätzliches Reduktionsmittel. Das Ziel: CO2-Emissionen reduzieren – denn im Gegensatz zu Kohlenstoff reagiert der Wasserstoff im Hochofen nicht zu CO2, sondern zu Wasser. Die erste vom Wirtschaftsministerium NRW geförderte Testreihe, die an einer Blasform des Hochofens 9 in Duisburg durchgeführt wurde, konnte erfolgreich abgeschlossen werden. Im Mittelpunkt standen insbesondere Erkenntnisse über die Anlagentechnik unter den Bedingungen des Wasserstoffeinsatzes.
Im Rahmen des vom Bundesministerium für Wirtschaft und Klimaschutz geförderten Reallabors H2Stahl wird der Wasserstoffeinsatz nun auf alle 28 Blasformen des Hochofens ausgeweitet. Forschungsziele sind unter anderem die Einflüsse industriellen Wasserstoffeinsatzes auf die metallurgischen Prozesse im Hochofen zu untersuchen sowie Parameter für einen effizienten Reduktionsmitteleinsatz zu entwickeln.
Das übergeordnete Ziel ist es, den Wasserstoffeinsatz als Brückentechnologie zur technischen CO2-Minderung an bereits bestehenden Hochofenanlagen zu verankern. Sofern grüner Wasserstoff in ausreichenden Mengen zur Verfügung steht, ist an einem Aggregat eine CO2-Minderung von bis zu 20 Prozent möglich. Grundlage der Förderung ist die Überzeugung, dass bei der Transformation des Energiesystems die Industrialisierung des Wasserstoffeinsatzes dabei
helfen wird, die deutsche Stahlindustrie nicht nur klimafreundlich, sondern auch zukünftig wettbewerbsfähig zu halten.
Im Rahmen der Erweiterung des Wasserstoffeinsatzes auf alle 28 Blasformen des Hochofens 9 wird zugleich die werksinterne Infrastruktur auf eine großindustrielle Versorgung mit Wasserstoff vorbereitet. Dies umfasst auch die Anbindung an die bestehende Wasserstoff- Infrastruktur von Air Liquide. Um eine kontinuierliche Wasserstoffversorgung des Hochofens zu sichern, wird vom Projektpartner Air Liquide eine rund sechs Kilometer lange Pipeline gebaut werden. Diese verbindet das Duisburger Stahlwerk mit dem Produktionsnetzwerk von Air Liquide.
Gilles Le Van, Vice-President Large Industries and Energy Transition Air Liquide Central Europe: “thyssenkrupp und Air Liquide bringen mit Wasserstoff an Europas größtem Stahlstandort Duisburg die Dekarbonisierung der Stahlerzeugung voran. Es ist Air Liquide eine große Freude, mit seinem Know-how dazu beizutragen, dass in der Stahlproduktion effektiver Klimaschutz und internationale Wettbewerbsfähigkeit miteinander vereinbar bleiben.“
Um den entscheidenden Technologiewechsel von der klassischen Hochofentechnologie zur wasserstoffbasierten Direktreduktion vorzubereiten, wird im Rahmen von H2Stahl außerdem eine Direktreduktions-Versuchsanlage gebaut werden. In der neu zu konzipierenden, vom BFI betriebenen und wissenschaftlich betreuten Anlage soll der Einsatz von wasserstoffhaltigen Prozessgasen in Kombination mit Erdgas und reinem Wasserstoff erprobt werden.
Neben marktüblichen Einsatzmaterialien für Direktreduktionsanlagen werden auch weitere eisenoxidhaltige Einsatzstoffe, bis hin zu potenziell geeigneten Reststoffen, zum Einsatz kommen. Für die wissenschaftliche Auswertung wird die Direktreduktions-Versuchsanlage mit zusätzlicher Messtechnik ausgestattet werden. Begleitet werden die Untersuchungen in der Direktreduktions-Versuchsanlage durch Modellierungen sowie Sonderuntersuchungen
im Technikum des BFI.
Im Vordergrund der geplanten Arbeiten stehen die Untersuchung der Reduktionsprozesse und der Verfahrensparameter, um einen reibungslosen Übergang auf die späteren Großanlagen zu gewährleisten.
„Die flexible Nutzung wasserstoffhaltiger Gase sowie unterschiedlichster eisenoxidhaltiger Einsatzstoffe in einem Direktreduktionsprozess ist eine Herausforderung. Die wissenschaftlichen Untersuchungen werden wesentliche Antworten zum sicheren und effizienten Betrieb der Prozesse sowie der geeigneten Betriebsparameter liefern“, sagt Michael Hensmann, Leiter der Abteilung Ressourcentechnologie Einsatzstoffe des BFI, und ergänzt: „Mit den im Reallabor H2Stahl geschaffenen Einrichtungen werden dringend erforderliche Untersuchungen für den klimafreundlichen Umbau der Stahlindustrie ermöglicht“.
thyssenkrupp plant die Fertigstellung der ersten industriellen Direktreduktionsanlage inklusive Einschmelzer für das Jahr 2025.
Der operative Start von H2Stahl markiert den nächsten wichtigen Meilenstein auf dem Weg zu einer klimaneutralen Stahlproduktion.
„Wir beginnen jetzt unsere Werksinfrastruktur auf den großindustriellen Einsatz von Wasserstoff vorzubereiten“, erläutert Dr. Arnd Köfler, CTO bei thyssenkrupp Steel. „Mit der Pipelineanbindung an die bestehende Wasserstoff- Infrastruktur von Air Liquide setzen wir außerdem einen weiteren Impuls, die Produktion von grünem Wasserstoff so schnell wie möglich hochzufahren. Der Bedarf ist da.“
Mit H2Stahl werden nicht nur wichtige Erkenntnisse für den Umstieg auf die Direktreduktion gesammelt: Durch den Wasserstoffeinsatz am Hochofen können – je nach Verfügbarkeit von grünem Wasserstoff – bereits erhebliche CO2-Minderungen erzielt werden.
„Mit H2Stahl verschränken wir zwei Phasen unserer Klimastrategie: zum einen die Industrialisierung des Wasserstoffeinsatzes im bestehenden hochofenbasierten Technologierahmen, einhergehend mit bereits erheblichen CO2-Minderungen in der Produktion. Und zum anderen die Vorbereitung der Direktreduktion durch den Aufbau der Infrastruktur und eine gründliche prozess- und verfahrenstechnische Vorbereitung“, ergänzt Köfler.
(Quelle: thyssenkrupp Steel Europe AG)
Schlagworte
Air LiquideAnlagenAnlagentechnikBundCO2CO2-EmissionenDekarbonisierungDeutschlandDirektreduktionDuisburgEinsatzstoffeEmissionenEnergieEnergiewendeErdgasEUForschungHochofenHochofenanlageIBUIndustrieINGKlimaschutzKlimastrategieMesstechnikMinisterium für WirtschaftNRWProduktionProzessgaseReduktionsmittelRoheisenRoheisenproduktionSchmelzeStahlStahlerzeugungStahlherstellungStahlindustrieStahlproduktionStahlwerkStrategieTechnikThyssenthyssenkruppThyssenkrupp Steel EuropeThyssenkrupp Steel Europe AGTransformationUnternehmenVDEhWasserstoffWasserstoffbasiertWettbewerbWirtschaftWirtschaftsminister